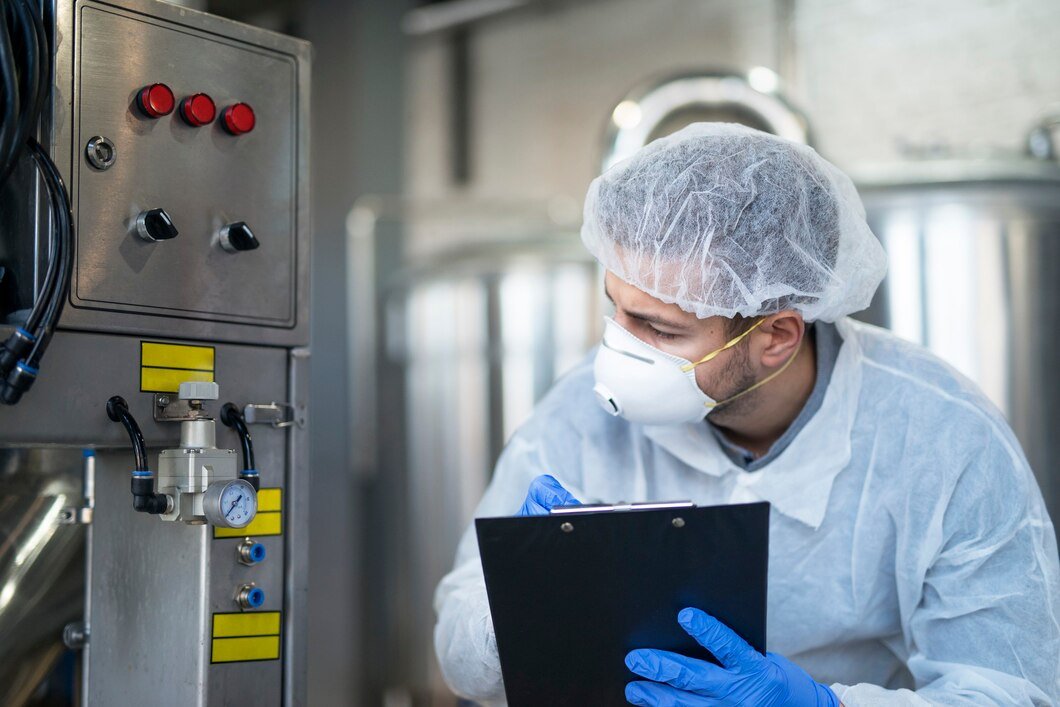
In the pharmaceutical industry, ensuring that medicines are safe, effective, and high-quality is extremely important. Quality Assurance (QA) plays a key role in achieving this goal. QA in pharmaceutical industry means making sure that every part of the medicine-making process, from the ingredients to the final product, meets the required standards. Let’s dive into how pharmaceutical companies implement effective QA protocols to maintain these high standards.
Steps to Implement Effective QA Protocols in Pharmaceutical Production
1. Set Clear Standards and Guidelines
Before starting any production, companies need to create clear standards for what the medicine should be like. These standards cover things such as how pure the ingredients should be, the correct way to mix them, and the final packaging. These guidelines are followed at every stage of production.
2. Use Proper Equipment
To make sure medicines are made correctly, pharmaceutical companies need the right equipment. This includes machines that measure ingredients, mix them properly, and package the final product. All equipment must be regularly checked and cleaned to avoid mistakes that could affect the medicine’s quality.
3. Train Employees Well
People who work in pharmaceutical production need to be properly trained. This includes understanding the QA guidelines, knowing how to use the equipment, and following safety measures. Employees are regularly trained to make sure they know what’s expected of them and how they can help maintain high-quality standards.
4. Check Raw Materials
Before production even begins, it’s important to check all raw materials (ingredients used to make the medicine). These materials must meet strict standards for purity and quality. If the raw materials are not of the correct quality, the final product will not be safe to use. Quality control checks are done on every batch of raw materials to ensure they are suitable for use.
5. Perform Regular Testing
During the production process, various tests are conducted to make sure the product is being made correctly. For example, a company might test the medicine to check if it has the right amount of active ingredients, or if it breaks down in the body the way it should. These tests help catch any mistakes before the product reaches consumers.
6. Follow Good Manufacturing Practices (GMP)
GMP is a set of guidelines that pharmaceutical companies follow to ensure the quality of their products. These practices include cleaning the production area, making sure workers follow hygiene rules, and having a clean and controlled environment. By following GMP, companies can reduce the chances of contamination or mistakes during production.
7. Document Everything
Every step of the production process must be carefully recorded. This includes noting down the results of tests, inspections, and any actions taken to correct problems. These records help to track the quality of the medicines produced and provide proof that all steps have been followed correctly.
8. Inspect the Finished Product
Once the medicine is ready, it goes through a final inspection to ensure that it’s safe for people to use. This inspection checks if the packaging is correct, if the labeling has the right information, and if the medicine has been stored properly. If the product passes all these checks, it’s ready to be shipped.
9. Handle Complaints and Feedback
Even after the medicine has reached consumers, QA doesn’t stop. Pharmaceutical companies listen to customer complaints and feedback about the medicine. If any problems are reported, the company investigates to see if there was an issue with production or quality control. This helps improve the process for future production.
The Importance of QA in Pharmaceutical Industry
QA in pharmaceutical industry is essential for ensuring public safety. If a medicine is not of good quality, it could cause harm to patients or even fail to treat the illness it’s designed for. By following strict QA protocols, pharmaceutical companies make sure that they provide effective and safe medicines. This helps build trust between the company and the people who depend on their products to get better.
Challenges in implementing QA in pharmaceutical industry
Implementing effective Quality Assurance (QA) protocols in the pharmaceutical industry is essential for ensuring the safety, effectiveness, and quality of medications. However, this process comes with its own set of challenges. Below are some common problems encountered during the implementation of QA protocols, as well as their corresponding solutions:
1. Problem: Inadequate Training of Personnel
Solution:
- Invest in Comprehensive Training Programs: Employees at all levels should undergo continuous training on the latest QA guidelines, industry regulations (such as GMP and FDA standards), and best practices. This ensures that every worker is fully equipped to handle the QA processes and is aware of their responsibilities.
- Hands-on Training: Provide practical, hands-on training using simulations or real-life scenarios so employees understand how to respond to QA issues when they arise.
2. Problem: Failure to Follow Standard Operating Procedures (SOPs)
Solution:
- Enforce SOP Compliance: Clearly define SOPs and ensure that all employees have access to them. Regular audits and inspections should be conducted to confirm compliance with SOPs.
- Automate Where Possible: Implement digital systems that prompt employees to follow SOPs, reducing the chance of errors in manual processes.
3. Problem: Inconsistent Raw Material Quality
Solution:
- Stringent Supplier Qualification and Auditing: Implement a robust process for selecting suppliers based on their ability to consistently deliver high-quality raw materials. Regular audits of supplier facilities are crucial to maintaining material quality.
- Material Testing: Perform incoming quality control tests on all raw materials before they are used in production. Establish stricter acceptance criteria for raw material quality and reject anything that doesn’t meet specifications.
4. Problem: Contamination During Manufacturing
Solution:
- Improve Cleanliness and Hygiene Standards: Establish rigorous cleaning protocols and ensure that production environments are sanitized regularly. GMP guidelines should be followed to ensure contamination prevention.
- Regular Equipment Maintenance: Ensure that manufacturing equipment is regularly maintained and inspected to prevent contamination. Use validated cleaning and sterilization techniques on all equipment and surfaces.
5. Problem: Lack of Proper Documentation and Record Keeping
Solution:
- Implement Digital Record Systems: Use digital tools for tracking, managing, and storing QA-related data, such as batch records, testing results, and inspection reports. This minimizes errors and ensures quick access to accurate data.
- Regular Audits: Conduct internal audits to ensure documentation is up-to-date and properly maintained. A culture of accountability should be developed to ensure all processes are documented correctly.
6. Problem: Inadequate Quality Control Testing
Solution:
- Implement Rigorous Testing Protocols: QA teams should conduct comprehensive testing at multiple stages of the production process, including raw materials, in-process samples, and final products.
- Expand Test Methodologies: Adopt a wide variety of testing methods, including stability testing, microbiological testing, and process validation, to ensure product quality is thoroughly assessed before release.
7. Problem: Compliance with Global Regulations
Solution:
- Stay Updated on Regulatory Changes: Ensure QA teams are aware of changes in regulations from local and international health authorities (such as the FDA, EMA, and WHO). Regularly review the regulations and incorporate them into the QA system.
- Cross-Functional Training: Collaborate with the regulatory affairs department to stay informed about changing standards and ensure the QA protocols are updated accordingly.
8. Problem: Product Recall Due to Quality Issues
Solution:
- Robust Traceability System: Implement a traceability system that tracks all aspects of production, from raw material sourcing to finished product distribution. This helps quickly identify and isolate any batch-related issues.
- Root Cause Analysis and Corrective Actions: After a recall, conduct a thorough investigation into the root cause of the issue. Implement corrective actions to prevent recurrence, and continuously improve QA protocols to minimize future risks.
9. Problem: Resistance to Change or QA Integration
Solution:
- Change Management Programs: Employees may resist adopting new QA protocols. It’s essential to implement structured change management programs that clearly communicate the benefits of the changes and address employee concerns.
- Leadership Support: Ensure that leadership actively supports and participates in the QA implementation process, setting an example for the rest of the team.
10. Problem: Data Integrity Issues
Solution:
- Data Validation Protocols: Implement procedures to verify that data is accurate, complete, and consistent across all stages of production. Regular audits should be carried out to ensure data integrity.
- Secure IT Systems: Protect QA data through secure, validated IT systems that track, record, and manage all quality-related data to prevent unauthorized access or manipulation.
11. Problem: Lack of Risk Management Framework
Solution:
- Implement a Risk-Based Approach: Develop and implement a risk management framework that prioritizes quality control efforts based on potential risks to product safety, efficacy, and regulatory compliance. This includes conducting risk assessments regularly to identify and address potential threats.
- Proactive Risk Mitigation: Use tools such as Failure Mode Effects Analysis (FMEA) or Hazard Analysis and Critical Control Points (HACCP) to identify, assess, and mitigate risks before they cause problems in the production process.
12. Problem: Inadequate Supplier and Vendor Management
Solution:
- Supplier Audits and Qualification: Conduct regular audits of all suppliers to ensure that they meet quality standards. Maintain strict qualification procedures to vet new suppliers before they are used for sourcing raw materials or components.
- Establish Clear Contracts and Expectations: Set clear expectations and quality standards in contracts with suppliers to ensure there is alignment between both parties regarding quality requirements.
Conclusion
In conclusion, implementing effective QA protocols in pharmaceutical production is vital for making sure that medicines are of the highest quality. By setting clear standards, using proper equipment, training employees, and following good practices, companies can create safe and effective medicines. Through constant testing, inspections, and feedback, the pharmaceutical industry ensures that patients can rely on the products they take. While there are numerous challenges in implementing effective QA protocols in the pharmaceutical industry, the solutions outlined above can help mitigate these issues. QA in pharmaceutical industry is not just about checking the end product. It ensure the entire production process is done correctly to protect the health and safety of consumers.