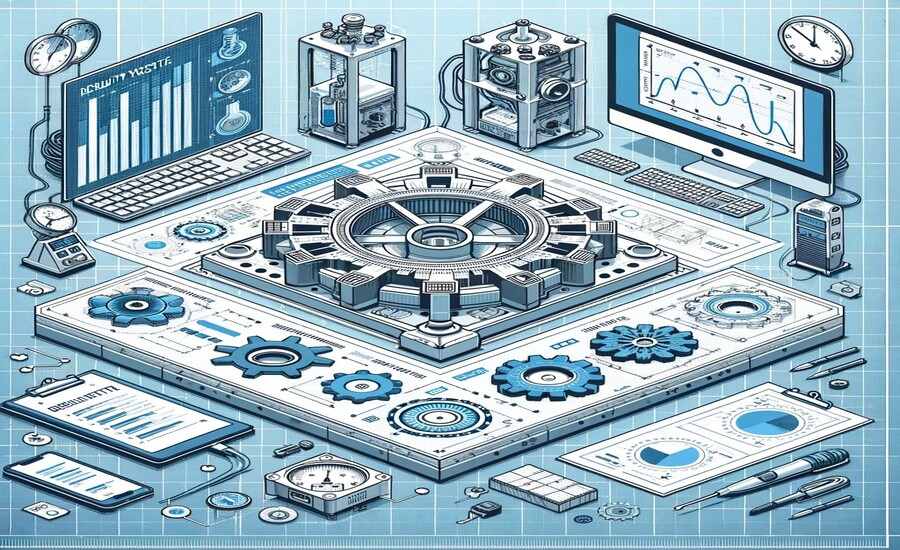
Reliability testing systems are key to product development and quality assurance processes in different sectors. These systems are intended to assess and guarantee the reliability of products, components, and systems during their expected lifetimes under anticipated or exceptional circumstances. The basic principles of reliability test systems, their importance, and the process involved in the design of the reliability testing system will be covered in this introduction.
What’s the reliability test system?
The reliability testing systems consist of methods, equipment, and software used to carry out tests to assess product or system reliability. To predict the behavior and performance of the product over time, these tests simulate various conditions, enabling manufacturers to identify potential failures before the product is placed on the market. The objective is to ensure that products satisfy industry standards and consumer expectations, intending to ensure consumer durability, safety, and reliability.
Importance of Reliability Test Systems
The use of reliability test systems is driven by the need to:
- Minimize Failure Risks: Early detection of design flaws or material weaknesses that could lead to product failures.
- Reduce Costs: Identifying and addressing issues early in the development cycle reduces the cost of repairs, recalls, and warranty claims.
- Comply with Regulations: Ensuring products meet regulatory requirements regarding safety and performance.
- Enhance Customer Satisfaction: Reliable products improve customer satisfaction and loyalty, which are crucial for a brand’s reputation and competitiveness.
The main components of the reliability test systems
1. Test Planning and Design
- Objective Setting: Define the aspects of reliability that are to be covered by tests, such as durability, lifetime or response under stress.
- Test Development: Design tests that accurately simulate the operating environment and stresses the product will face.
2. Execution of Reliability Tests
- Operational test: tests the product through a typical usage scenario to identify operating failures.
- Environmental testing: To ensure stability, the product must be exposed to extreme temperatures, humidity, vibration, and other environmental factors.
- Life test: measures the length of time that product lasts in ordinary or accelerated conditions before it fails.
3. Data Collection and Analysis
- Data collection: collect data on the product’s performance in testing, identifying any failures and conditions that have caused them.
- Statistical Analysis: Use statistical methods to analyze data, predict reliability outcomes, and determine the product’s mean time to failure (MTTF) or mean time between failures (MTBF).
4. Feedback and Improvement
- Feedback integration: improving product designs, materials or manufacturing processes using knowledge acquired during testing.
- Continuous improvement: reliability tests are not over once the product has been launched. The continuous testing of new technologies and changing consumer needs help to cope with these changes.
Application Across Industries Reliability test systems are applied in virtually all production sectors, including motor vehicles, aeronautics, electronics, consumer goods, and healthcare. Each industry may lay down specific reliability test standards reflecting the specific requirements and safety requirements of its products.
Designing a Reliability Test System
The design of an effective reliability test system is a key step that directly affects a product’s potential success in terms of performance, durability, and customer satisfaction. This article provides an overview of the process and considerations involved in designing a reliability testing system.
Understanding the Requirements
The first step in designing a reliability test system is to thoroughly understand the product’s functionality, the environments in which it will be used, and the potential stresses it will encounter. This includes:
- Product Specifications: Detailed knowledge of the product’s design, materials, and operational parameters.
- Usage Scenarios: The different ways in which consumers will use the product could affect its performance and lifespan.
- Environmental Conditions: Conditions under which the product must operate, including temperature ranges, humidity levels, mechanical stresses, etc.
Setting the Objectives
Clear objectives guide the design of the reliability test system and ensure that the testing is aligned with the product’s goals and the company’s business strategy. Objectives might include:
- Identifying Failure Modes: Understanding how and why a product might fail under certain conditions.
- Validating Design Specifications: Confirming the product meets all design and performance specifications.
- Estimating Product Life: Determining the product’s expected lifespan under normal usage conditions.
Developing the Test Plan
A comprehensive test plan lays out the blueprint for conducting the reliability tests and includes:
- Selection of Test Methods: Choosing appropriate test methods that simulate real-life usage and environmental conditions.
- Sampling: Determining the number of units to test and the criteria for selecting these units.
- Scheduling: Timeline for each test phase, considering product development stages and market launch dates.
- Resource Allocation: Assigning personnel, equipment, and budget needed for the testing.
Designing Test Procedures
Test procedures detail the step-by-step methodology for conducting each test. This involves:
- Standard Operating Procedures (SOPs): Detailed instructions on how to set up and perform each test.
- Safety Protocols: Ensuring all safety measures are in place to protect personnel and equipment during testing.
- Data Collection Methods: Techniques for accurately capturing data such as temperatures, stress levels, and failure rates.
Implementing the Test System
Once the design is complete, the next step is implementing the test system. This includes:
- Building or Acquiring Test Equipment: Depending on the specific needs, this may involve custom-building test equipment or purchasing standard test systems.
- Training Personnel: Ensuring all personnel involved in the testing are fully trained on the procedures and understand the safety protocols.
- Pilot Testing: Conduct a trial run to ensure the test system works as planned and refine the procedures if necessary.
Continual Review and Optimization
A reliability test system is not static; it should evolve with the product and the market conditions. Regular reviews and updates to the testing procedures are necessary to adapt to new findings, technological advancements, and changes in consumer behavior.
- Analyzing Test Results: Regular analysis to draw actionable insights and make informed decisions on product improvements.
- Feedback Loop: Integrating feedback from the reliability tests into product development to enhance design and performance.
Conclusion
Reliability testing systems are indispensable to ensure that products comply with the design specifications and satisfy customers’ expectations of performance and longevity. Businesses can protect their investment, enhance market reputation, and secure the safety of consumers through rigorous product quality tests and validation. The sophistication and importance of reliability testing systems will continue to increase as technology evolves, making them a key element of the product development and maintenance cycle.
It is a complicated but essential process to plan and analyze the product and its environment in detail and a clear understanding of test objectives that must be followed when developing reliability testing systems. Companies can significantly increase their chances of success in the market and strengthen trust and customer satisfaction by carefully developing a test system to deal with all possible problems that products may face.