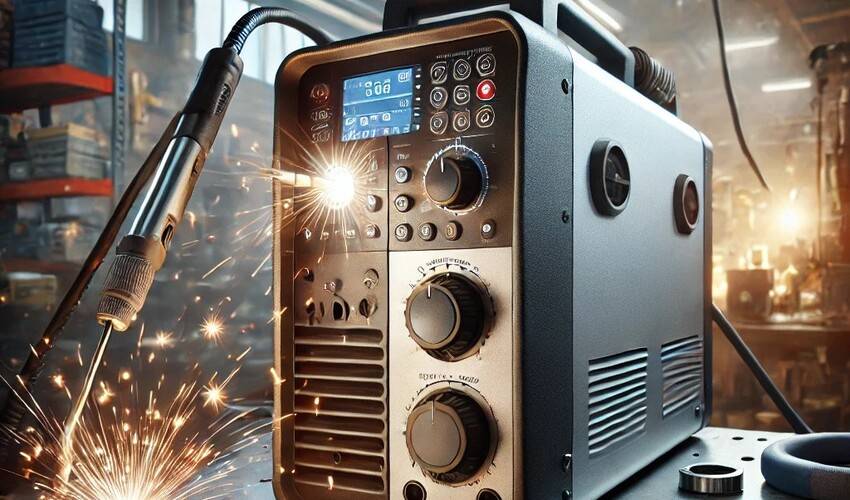
Gas metal arc welding machine : what is it?
GMAW also referred to as Metal Inert Gas (MIG) uses an electric arc between the wire and the base metal. The heat produced by the arc fuses the two surfaces and the wire used to produce a pool of molten material which on solidification forms the weld. Originally introduced during the World War II in the 1940s, gas metal arc welding machine has advanced and is now one of the most favored processes of welding due to its speed and convenience.
Parts of a gas metal arc welding machine Machine
A typical GMAW machine comprises several key components:
- Power Source: Provides the required amount of electrical energy necessary for the formation of the arc.
- Wire Feed Unit: A consumable wire having weld metal is fed into the welding gun at a controlled rate.
- Welding Gun: Plays the wire and shielding gas towards the weld joint.
- Gas Supply System: Serves as a shroud to safeguard the puddle from the impact of the surrounding environment.
Types of GMAW Machines
Gas metal arc welding machine machines come in various types to suit different welding needs:
Manual GMAW Machines: Expect the operator to manage as many factors as are possible with respect to welding.
Semi-Automatic GMAW Machines: It incorporates the feature of wire feeding automation but for the welding gun, control is done manually.
Fully Automatic GMAW Machines: Retrieve robotic arms and sectorial control for reproducible excellent welds.
Working Principle of GMAW
The GMAW process involves several steps:
Arc Initiation: On pulling the trigger of welding gun, then the power source creates an electric arc between wire electrode and the weldment.
Metal Transfer: The wire electrode becomes molten and dips into the weld pool picking molten metal.
Shielding Gas: Sheltering gas for example argon or CO2 is encouraged through the welding gun to avoid oxidation or other external contamination on the weld.
Solidification: The material of the two components melts at the joint and the pool solidifies to give a critical interface.
Advantages of GMAW Machines
GMAW machines offer numerous benefits:
Efficiency: It has high deposition rates as well as high welding speeds.
Precision: Welds that are more uniform as well as of very good quality with fewer defects. User-Friendly: Easy to learn and operate, making it accessible to both novice and experienced welders.
Versatility: Can be applied to different types of metals such as, aluminum, steel as well as, stainless steel.
Applications of GMAW
GMAW is used in a wide range of industries:
Automotive Industry: It has a hammering as well as cutting option for joining car frames and welding exhaust systems and other parts.
Construction: For structure steel and other building elements that is construction infrastructure.
Shipbuilding: To building and do ship and offshore platforms repair work.
Aerospace: For the fabrication of various parts and subassemblies of an aircraft as well as various structural members.
Fabrication: When developing products made of metal and their assembles in particular.
Selection Criteria of GMAW machine
When selecting a GMAW machine, consider the following:
Welding Projects: Define the material categories you will be welding and their common thicknesses.
Budget: But since this product is aimed at business, then it is necessary to balance the price for performance and functionality
Brand Selection: Select brands that go with quality and reliability that are in the market and are well known.
A GMAW machine arrangement involves selection of the most suitable mode of usage depending on the case in hand together with other relevant parameters.
Setting Up a GMAW Machine
Follow these steps for a successful setup:
Read the Manual: Read and comprehend the manufacturer’s guidelines and requirement.
Safety Precautions: Ensure you wear an apron, gloves and most importantly a welding helmet.
Initial Setup: According to the manual, fix the power source, wire feed unit, the welding gun and the gas supply system.
Adjust Settings: Customize your welds by adjusting the voltage, wire feed rate, and gas flow that corresponds to your welding application.
GMAW Welding Techniques
Different techniques can be employed based on the material and position:
Material-Specific Techniques: Tweak for aluminum, stainless & carbon steel.
Position Welding: Methods used in welding such as the flat, horizontal or vertical and overhead positions.
Pulse Welding: It is advisable to employ pulsed current because it provides more control and has a reduced amount of spatter.
Common Issues and Troubleshooting
Address common problems with these solutions:
Wire Feed Problems: Check positions and tensions of the wire feed unit is appropriate or not.
Poor Arc Stability: Make sure voltage is stable and that the contact tips are clean.
Spatter Control: Reduce the flow rate and the voltage, the adjustment that will be used to prevent spatter.
Maintenance of Machines
Regular maintenance is crucial for optimal performance:
Routine Checks: check cables, connectors and all the other attached components for signs of wear or signs that will show that it has been damaged.
Cleaning: In addition the machine and component needs to be cleaned because contamination is an issue that should be avoided.
Replacing Consumables: Replace the contact tips, nozzles and wire often so that you can achieve good weld outcomes.
Safety Measures in GMAW
Ensure safe welding practices:
Protective Gear: Put on proper personal protective equipment.(PPE).
Proper Ventilation: Make sure there is enough fresh air to prevent suffocation by the toxic gases that may be produced. Handling Equipment Safely: The following tips are one way of observing safety measures while handling and using welding equipment:
Compare GMAW with other welding techniques:
TIG Welding: Provides a higher level of accuracy when used but it is slower and whereby its usage is more complicated.
Stick Welding: It can be used outdoors due to the reduced amount of fumes produced but creates a lot of spatter and the electrodes get consumed frequently.
Flux-Cored Arc Welding: Much preferred when cutting through thick material but produces a lot of smoke and has to be followed by wiping.
Innovations in GMAW Technology
Recent advancements include:
Automation: Robots and other forms of automation for the preparation and ensure of numerous constant and high quality welds.
Robotics Integration: New accuracy and productivity due to the installation of robotic arms.
Advanced Controls: New designs to make operating user interfaces and control systems better.
Economic effects of GPIO GMAW machines
The economic benefits of Gas metal arc welding machine include:
Cost-Benefit Analysis: Even though it may require a large amount of money to invest at the start of the project, there is a huge saving in the long run in terms of labor costs and raw material.
Industry Growth: Increased demand for the employed personnel such as skilled welders, and enhanced welding technology used in the process.
Job Creation: New opportunities in the areas of manufacturing, construction and so on.
Environmental Impact of GMAW
GMAW promotes sustainable practices:
Emission Control: Such techniques include the use of clean shielding gases in order to reduce some of the emissions.
Energy Efficiency: Less energy is used compared to other welding processes, Alternative sources of energy can be used during the welding process.
Sustainable Practices: Disposing of consumables and items in the right way and reusing items where possible.
Future Trends in GMAW
Predictions for the future of GMAW technology include several key developments:
Emerging Technologies: Future developments that might be witnessed in welding technologies are constant improvements and even incorporation of AI and ML to make the processes more accurate and streamlined.
Automation: More adaptations of an automated system and even robotics for welding will be made so that fewer people will intervene in the welding process while maintaining preciseness and quality.
Environmental Sustainability: It is also predicted that it will pay more attention to environmental issues, for example, emission cutting, energy utilization promotion, and green materials and technologies application.
Applications of GMAW to Industries: A Review
Automotive Industry: Some of the industries adopting Gas metal arc welding machine include the automobile industries like Tesla and Ford where they apply the process when joining car frames and exhaust systems due to the high and accurate rates the process provides.
Construction: In constructional projects particularly where there are big structures being constructed GMAW is widely used in welding structural steel.
Aerospace: Boeing the industry’s aerospace manufacturing company utilizes GMAW for welding of airplane parts in order to obtain top quality joints in view of safety.
Shipbuilding: Manufacturing plants including the ship manufacturing unit of Maersk use GMAW so as to build and redesign ships since tough and strong welds are required.
Frequently Asked Questions
What is a GMAW machine?
A gas metal arc welding machinemachine is a machine that is commonly used in gas metal arc welding which is a method of welding where the electric arc is generated between metal and consumable wire electrode and the workpiece metal producing a weld pool that on being cooled solidifies the joint.
What are the differences that GMAW can be distinguished from other welding technologies?
In comparison to the mechanisms such as TIG and Stick welding, GMAW is more effective and provides a higher welding rate with a superior quality of weld free from spatter hence less cleaning.
What are the major subassemblies of a GMAW machine?
They include the power source, wire feed unit, welding gun and the gas supply system.
What is shielding gas used for in GMAW?
The shielding gas prevents the penetration of atmospheric gases into the weld pool and thus there is no oxidation of the weld pool thus giving the welder a clean joint.
Is it possible to use GMAW on all kind of metals?
GMAW is adaptable to many options in metals which include aluminum, stainless steel and the carbon steel.
Here are some precautions that should be taken when operating the GMAW machine Safety measures.
To reduce harm always put on necessary protective gear, check for airflow and the operating instructions from the manufacturer.
Conclusion
GMAW machines are among the most effective and versatile welding machines that have improved the welding industry a lot. With time, the growth in use of GMAW machines will be even more evident in car manufacturing, construction, aircraft manufacturing, and shipbuilding industries. Because knowledge and appreciation of the characteristics, operational concepts and uses of GMAW machines, can tremendously increase utility and promote the achievement of the welding goals securely and efficiently.